Resources
Browse our latest news, opinions and resources, or find upcoming events to attend.
News and insights
Jul 26, 2024 11:14:04 AM
Join Paul Davis, CEO of First Light, and Felipe Munoz, analyst at JATO, as they discuss the dominance of Chinese EV makers, challenges for Western brands, and the impact of trade policies. Learn how cooperation can drive innovation and growth in the global automotive market.
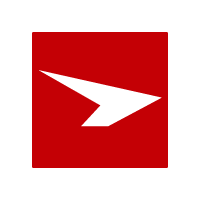
Jul 16, 2024 3:13:21 PM
Learn how JATO leverages data standardization and advanced data architecture to provide competitive insights and enhance business intelligence in the automotive industry.
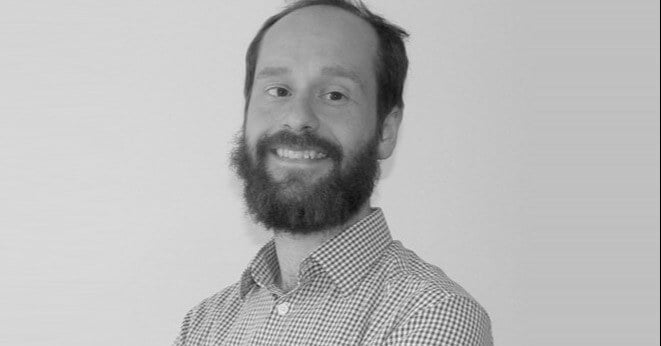
Jun 26, 2024 11:50:00 AM
Explore insights into the Indonesian automotive market, including the strategy of Chinese automakers and the latest automotive data from JATO. This analysis highlights market saturation and explores missed opportunities in one of Southeast Asia's largest car markets.
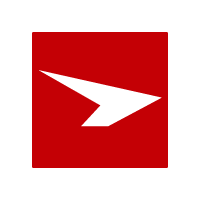
Reports and whitepapers
17 July 2024
Gain insights into the growth of China OEMs and their role in shaping the automotive industry. Analyze key players and emerging trends in JATO's latest report.
By Felipe Munoz
17 July 2024
Delve into Norway's pioneering role in the electric vehicle market, focusing on battery electric and plug-in hybrid electric vehicles, and its lessons for global automakers.
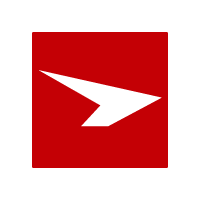
05 June 2024
Southeast Asia remains a relatively untapped market for ev's. With growing consumer demand for NEVs across the region, we examine the landscape.
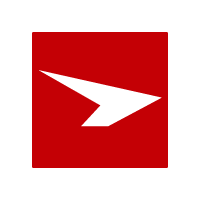
JATO Podcast
Nov 6, 2023 10:44:27 AM
JATO Podcast | Episode 4 | An interview with Polestar: the challenges and opportunities of introducing a new brand into Europe
An interview with Alexander Lutz, managing director of Polestar Italy. Learn how the brand succeeded in a crowded market, new products in development, and thoughts on an all-electric future.
May 17, 2024 9:25:19 AM
Listen to JATO’s podcast 7 featuring Felipe Munoz and Hormazd Sorabjee as they discuss the challenges and opportunities for global automakers and luxury car brands in India’s car market.
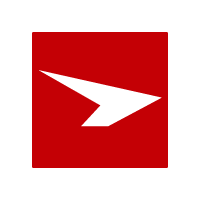
Apr 29, 2024 11:53:00 AM
Discover the future of mobility with our latest podcast episode featuring Merlin Ouboter. Gain insights into emerging trends, electric vehicle innovation, and sustainable transportation solutions. Presented by Felipe Munoz, this episode offers a glimpse into the future of mobility.
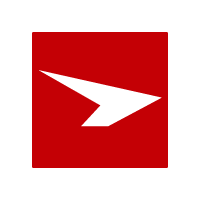
Mar 1, 2024 11:54:00 AM
Explore the dynamic landscape of Europe's automotive market in 2023 with JATO Podcast Episode 5. Join Felipe Munoz and guest Julian Rendell from Autocar as they discuss the surge in electric vehicles, the impact of Chinese automakers, and insights into European market.
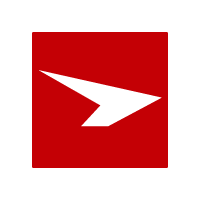
Media and press releases
18 July 2024
Explore JATO Dynamics’ data on how European BEV demand is slowing and the rise of Chinese car brands in the electric vehicle market. Stay updated with the latest EV market insights.
27 June 2024
European BEV demand fell 11% in May, with 19% of registrations from China. MG outsold Tesla despite losing ground. JATO Dynamics reports a 2.5% decline in new car registrations compared to last year, highlighting opportunities for Chinese OEMs in Europe amid high BEV prices and upcoming tariffs.
13 June 2024
Explore the Tesla Model Y's rise to the world's best-selling car of 2023. Learn from JATO Dynamics data about this electric SUV and its impact on the automotive industry.
30 May 2024
Explore the shifting trends in Europe's automotive market with JATO Dynamics. From electric vehicles and SUVs to Chinese-made cars, discover the evolving landscape and key insights into the latest market dynamics.
Webinars and events
May 30, 2023 4:35:25 PM
In this webinar recording our industry experts will delve deeper into our solution with focus on visualisations, delivery methods and real life data examples. Whether you're looking for a top-level snapshot of the market or want to deep dive into specific segment, Monthly Payments is the dataset for you.
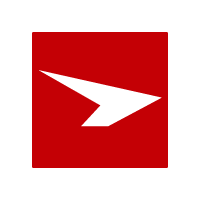
Mar 3, 2023 3:31:40 PM
Learn how you can put yourself in the shoes of your customers to better understand their car financing decisions. Watch the webinar recording to hear our automotive market experts discuss how you can provide captivating offers and stay current in the automotive finance space.
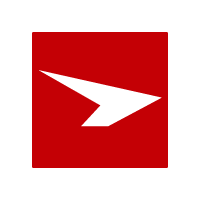
Feb 15, 2023 3:21:16 PM
In this webinar our insurance expert shared their unique perspective on the market, and talked about the blind spot automotive insurer are currently facing.
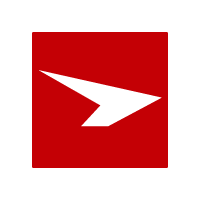
Newsletter
Jul 3, 2024 5:03:47 PM
Subscribe to JATO’s monthly Strategy & Innovation Newsletter, bringing the latest industry news round-up to your inbox.
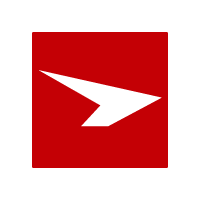
Jun 5, 2024 4:15:30 PM
Subscribe to JATO’s monthly Strategy & Innovation Newsletter, bringing the latest industry news round-up to your inbox.
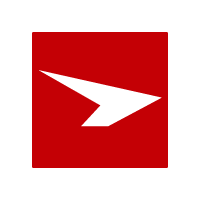
May 3, 2024 10:48:29 AM
Subscribe to JATO’s monthly Strategy & Innovation Newsletter, bringing the latest industry news round-up to your inbox.
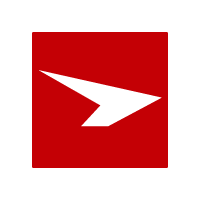
Our knowledge is your power. Connect with us.
Find out more about our specialist solutions for the automotive industry.
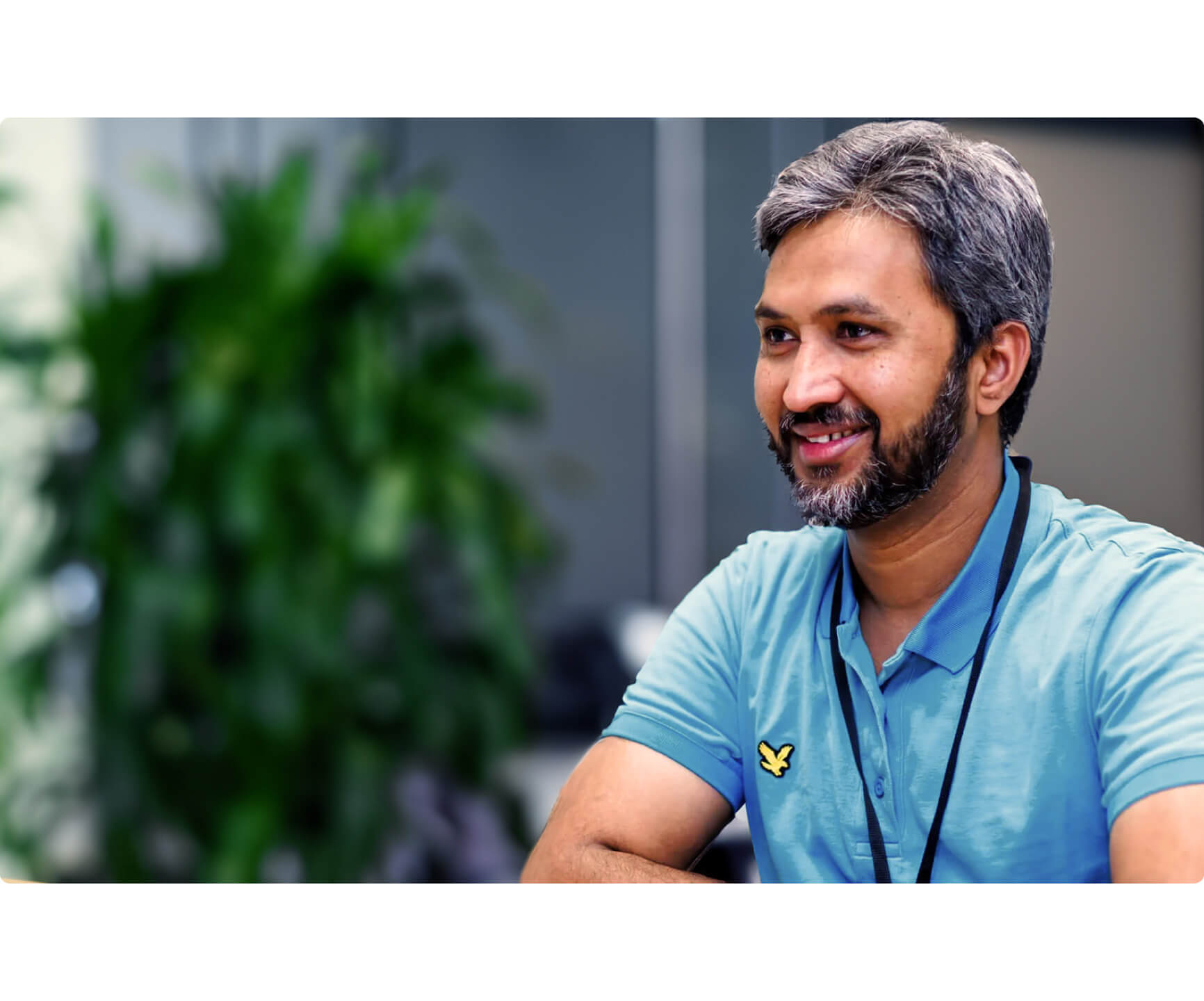